
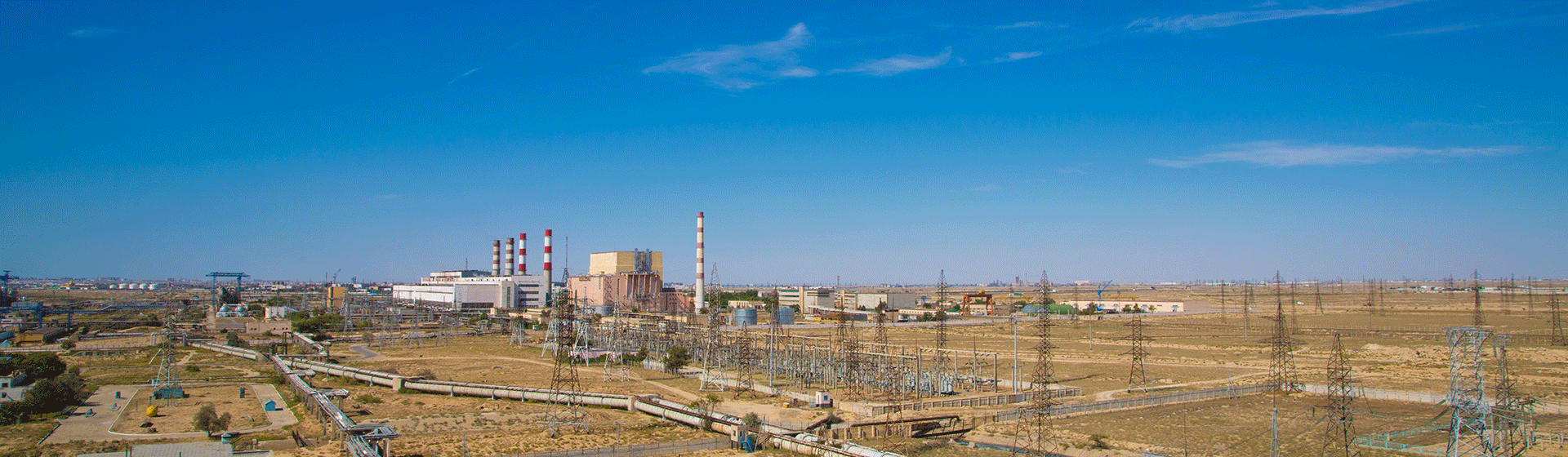
Что предстояло сделать?
Специалистам предстояло обследовать состояние водно-химического режима (ВХР) с применением реагентов аммиака, гидразингидрата, едкого натра и трилона Б на энергоблоках №№ 1,2, а также состояние ВХР с применением реагента Хеламина, аммиака и едкого натра на энергоблоке № 3.
Основной задачей водно-химического режима на станции является обеспечение надежной и экономичной работы теплосилового оборудования путем предотвращения образования отложений и накипи на поверхностях основного и вспомогательного оборудования и уменьшения коррозии на всех участках пароводяного тракта.
С какими проблемами столкнулись?
Проведенный анализ параметров работы и показателей водно-химического режима показывает, что в целом показатели питательной и котловой воды чистого и соленого отсеков, насыщенного и перегретого паров Энергоблока №№1,2 выдерживались в пределах установленных нормами ПТЭ.
В момент проведения обследования энергоблока №3, после длительной эксплуатации хеламинного режима (более 13 лет), наблюдалась тенденция ухудшения режима работы котлоагрегата №3 (увеличения удельной зашламленности поверхностей нагрева, забивание непрерывных продувок, увеличение внеплановых остановов котла).
После подробного анализа работы энергоблока №3 в период с 2006 по 2018 годах, специалистами компании «Asia Water Service» выявлено, что в 2006 году средняя за месяц величина непрерывной продувки составила 0,7 % при средней производительности котла 260 т/ч, в данный момент происходит переход режима с аммиачно-трилонного водного режима на реагентный, в качестве реагента был выбран Хеламин. В период с 2005 по 2010 годах наблюдается снижение удельной зашламленности поверхностей нагрева на 36,3 % по огневой стороне и 40,4 % по тыльной стороне, сократилось содержание меди в отложениях с 2,96 – 3,8% до 1,53 – 2,85% по тыльной стороне и с 3,07 – 3,84% до 1,47 – 3,28% по огневой стороне.
В 2007 году происходит увеличение производительности котла до 300 т/ч, непрерывная продувка при этом уменьшается и равна 0,6 %. В период 2008 - 2009 гг. происходит увеличение средней производительности котла до 360 т/ч, непрерывная продувка при этом уменьшается до 0,5 % (зафиксировано снижение непрерывной продувки котла ниже нормы: апрель – 0,46% (средняя производительность – 336 т/ч), июль – 0,46% (средняя производительность – 370 т/ч), август – 0,42% (средняя производительность – 415 т/ч). В результате увеличения производительности котла и ненормированной выдержки непрерывной продувки в 2009 году привело к забиванию линий непрерывных продувок.
27.01.2009 года выдается распоряжение № 131 «Временно, до особого распоряжения, периодическую продувку чистых отсеков (ЧО) КА№3 производить по графику ПТМ, а периодическую продувку соленых отсеков (СО) КА№3 проводить три раза в неделю». В период 2009 года средняя производительность котла составляла 360 т/ч, непрерывная продувка увеличилась до 0,9%, но при этом, в том же году, а точнее 03.08.2009, 14.09.2009 происходит забивание трубок непрерывной продувки КА №3.
19.03.2010 г. было выдано распоряжение № 176 «Непрерывную продувку КА№3 держать 1,5% от паропроизводительности, периодическую продувку экранных труб котла проводить три раза в неделю (время продувки по каждой точке выдерживать не менее 45 сек)», но при этом среднее значение непрерывной продувки составило 1,0%, при средней производительности 365 т/час. В этом году так же зафиксировано повторное забивание линий непрерывной продувки 08.03.2010, 04.08.2010. В период с 2011 по 2014 гг. средняя производительность котла составляла – 400 т/ч, непрерывная продувка – 1,12%. В этот период (13.04.2011, 11.09.2014, 13.11.2014) происходит забивание линий непрерывных продувок котельного агрегата №3. В феврале 2013 года зафиксировано регулярное снижение непрерывной продувки в среднем до 0,36 %, ниже допустимой величины – 0,5 %, при производительности 424 т/ч, данный случай зафиксирован в сентябре 2013 года 0,47% при производительности 430 т/ч.
В период с 2010 по 2014 гг. с ростом паровой нагрузки с 360 до 458 т/ч и теплового напора на экранные трубы произошло значительное увеличение удельной зашламленности поверхностей нагрева. Удельная зашламленность внутренней поверхности образцов труб чистого отсека составила с огневой стороны 237,0 – 404 г/м2, в зоне максимальных тепловых потоков до 528 г/м2 (фронт труба №113), с тыльной стороны 126,0 – 280,0 г/м2. По солевому отсеку отложения на поверхностях нагрева крайних труб в панели в зоне наибольшего теплового потока составили с огневой стороны 2490 – 3300 г/м2, а с тыльной 414 – 925 г/м2. Отложения носят локальный характер.
С ростом тепловой нагрузки произошло значительное увеличение доли содержания меди на крайних в панелях соленого отсека в среднем с 4 % до 52,0 – 66,0%.
В результате увеличения удельной зашламленности экранных труб КА №3 в период с 2010 г. по 2016 г., увеличились внеплановые остановы котла за данный период. Тенденция образования свищей возникает в основном на солевых отсеках. Локализация образования свищей наблюдается на уровне второго яруса горелок 8,5 – 9,0 метров, в зоне наибольшего теплового потока, в зонах сварочных стыков экранных труб.
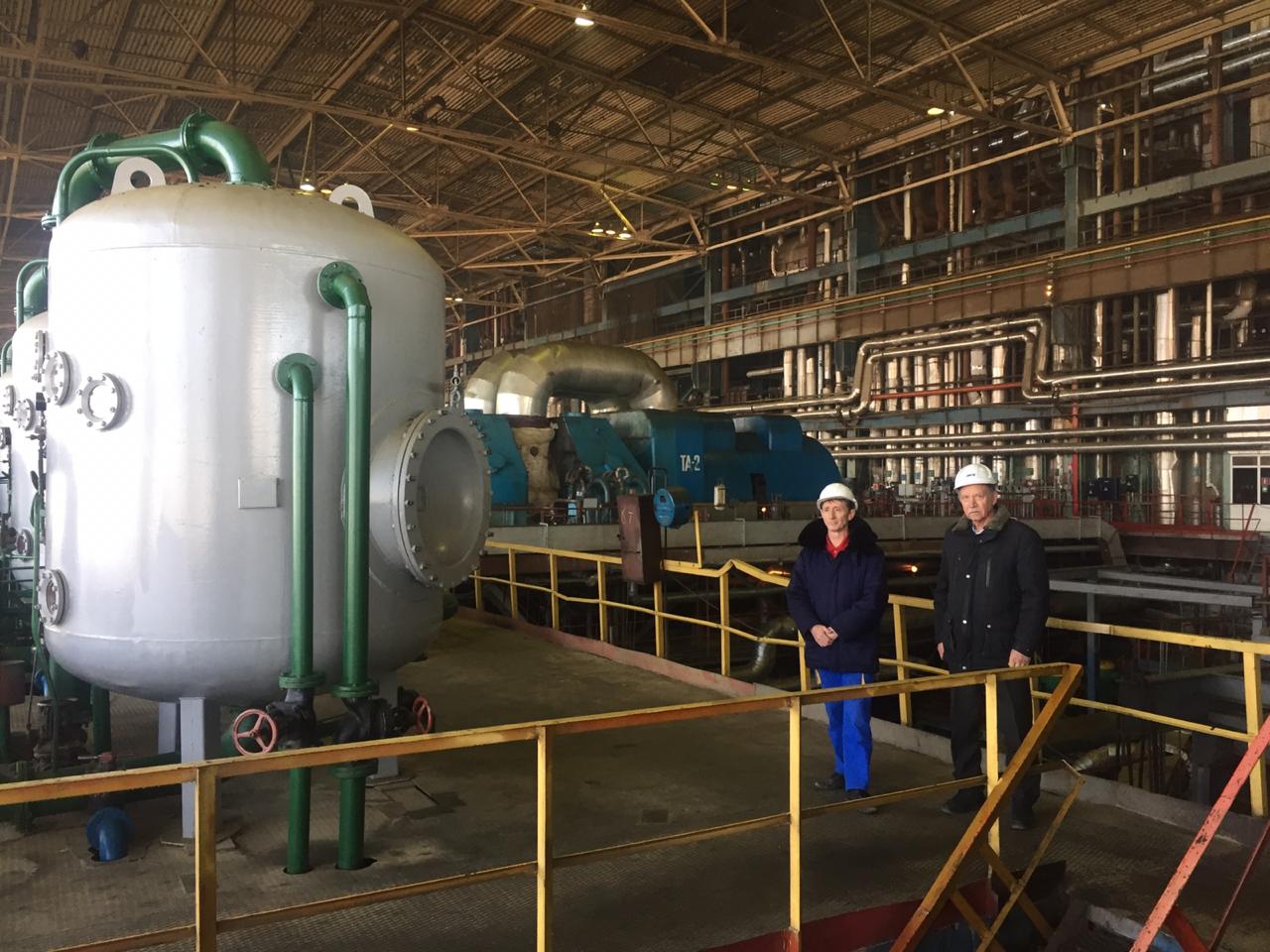
В период с 2006 по 2008 г. интенсивного вымывания отложений с экранных труб не зафиксировано, вероятнее всего происходило концентрирование растворимых продуктов отложений в местах вялой циркуляции котловой воды, на наклонных участках, где возможно расслоение потока пароводяной смеси (например, в трубах подового экрана или аэродинамического выступа на выходе из топки), в зонах непосредственно примыкающих к экономайзеру участку экрана. Увеличение производительности котла и ненормированная выдержка непрерывной продувки вероятнее всего интенсифицировало промывку питательного тракта и растрескиванию защитной пленки на теплонапряженных участках, после чего начался процесс вымывания отложений более интенсивно, что привело к забиваниям непрерывных продувок.
Увеличение производительности и большой диапазон изменения непрерывной продувки резко повлияло на уровень вскипания, вследствие чего увеличилась тепловая нагрузка на экранные трубы солевых отсеков, в результате произошло растрескивание защитной пленки на теплонапряженных участках, с образованием критических зон. Повреждаемость защитных пленок связано преимущественно с частыми теплосменами. Неблагоприятное сочетание условий, возможно, прежде всего, в зонах наброса или ударного воздействия на экраны топочного факела, стимулирующего дестабилизацию режима устойчивого пузырькового кипения из-за бурного парообразования со слиянием пузырьков пара в отдельные «лоскуты» паровой пленки, так называемое режим ОПК – «отход от пузырькового кипения». Режим ОПК вызывает значительное концентрирование у теплоотдающей поверхности растворимых примесей котловой воды, а также частые циклические колебания температуры металла на узко локализованном участке нестабильного кипения. Эти колебания способствовали повреждаемости защитных пленок, в результате чего произошел непосредственный контакт реакционной среды со свежеобразованной поверхностью «обнаженного» металла, на данных участках возможно развитие, с различной скоростью, но безостановочно, процессов пароводяной коррозии металла экранных труб.
В период с 2015 г. по 2018 г. паропроизводительность КА №3 варьировалось в пределах 400-490 т/час, резких скачков по производительности не наблюдалось, непрерывная продувка в среднем была равна 1,6 %, больших колебаний зафиксировано не было.
Каков выход из положения?
Рекомендации по энергоблокам №№ 1,2
Рекомендуем предусмотреть схему периодической кислотной промывки загрязненных свыше 400 г/м2 экранных панелей от отложений методом «травления».
Для обеспечения безопасного ведения ВХР предусмотреть автоматическую дозацию следующих реагентов: гидразин-гидрат, едкий натр, аммиак, трилон Б. Не допускать подачу конденсата в питательную воду всех котельных агрегатов без очистки на БОУ.
Наладить режим удаления кислорода в конденсационных установках. В противном случае повышенное содержание кислорода может привести к коррозии внутренних поверхностей оборудования и трубопроводов.
Для обеспечения более корректного ведения водно-химического режима необходимо обновить и доукомплектовать ЭБ №№ 1,2 приборами автоматического химического контроля.
Учитывая положительный, безаварийный опыт гидразинно-аммиачного водно-химического режима (ГАВР) с коррекционной обработкой котловой воды гидроксидом натрия и периодическим трилонированием, специалисты рекомендовали продолжить ведение ВХР данным методом.
Рекомендации по энергоблоку №3
Ввиду более стабильного гидразинно-аммиачного режима режима с коррекционной обработкой котловой воды гидроксидом натрия и периодическим трилонированием, специалистами рекомендовано перевести Энергоблок № 3 с Хеламинного режима на ГАВР.
Восстановить схему дозирования гидразина, трилона Б. Для корректировки рН питательной воды использовать аммиак, для корректировки рН котловой воды предусмотреть дозирование едкого натра в котловую воду.
Наладить режим удаления кислорода в конденсационных установках, т.к. повышенное содержание кислорода может привести к коррозии внутренних поверхностей оборудования и трубопроводов, что приведет к увеличению повреждений оборудования, снижению экономичности работы оборудования, из-за внеплановых остановов.
Не допускать подачу конденсата в питательную воду котельного агрегата без очистки на БОУ.
Для обеспечения более корректного ведения водно-химического режима необходимо обновить и доукомплектовать ЭБ № 3 проборами автоматического химического контроля.
Предусмотреть схему периодической кислотной промывки загрязненных свыше 400 г/м2 экранных панелей от отложений методом «травления».
Перед выводом блока в ремонт проводить консервацию экранных поверхностей котла.
Во время капремонта рекомендовано проводить вырезку образцов из различных поверхностей котла для определения количественного и качественного состава отложений.
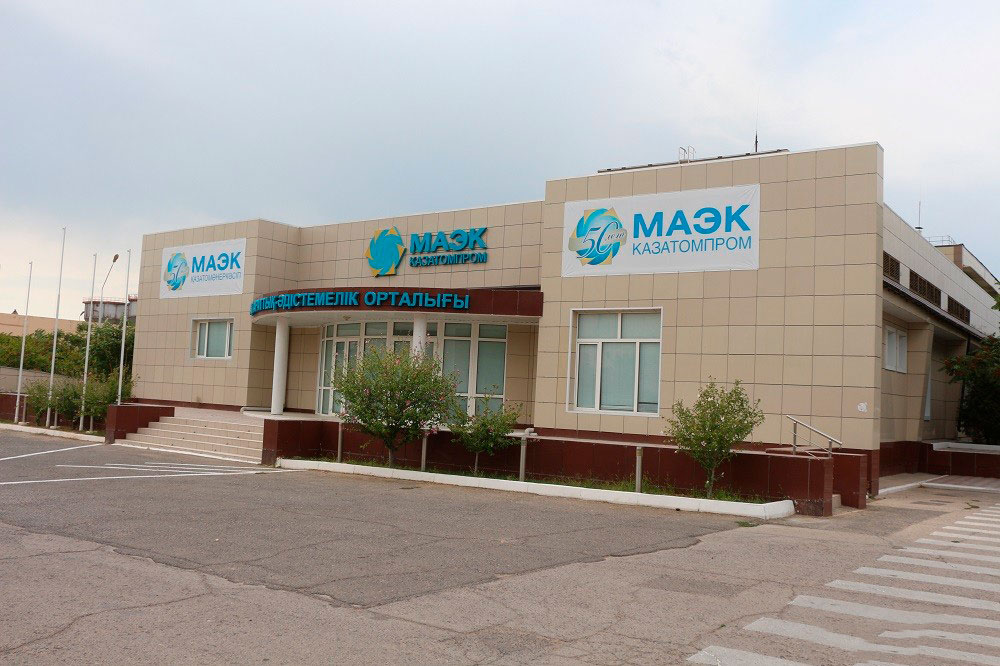